SHT36/42 Wiring
The free blue heatsink should be attached to the 2209 driver!!!
SHT36 and SHT42 only differ in appearance and installation size, otherwise, there is no difference. The usage method of SHT42 is the same as SHT36, here we only introduce SHT36.
Terminal Resistor Configuration
Before using CAN, please correctly configure the CANBUS terminal resistors.
- In a CANBUS bus protocol, there must be and can only be two 120-ohm resistors on a bus
- No matter how many USB devices you connect, as long as they are on the same bus, only two 120-ohm resistors are configured. Do not add a resistor for each device
- After connecting the CAN H and CAN L signal lines, use a multimeter to measure between CAN H and CAN L, the resistance should be about 60 ohms
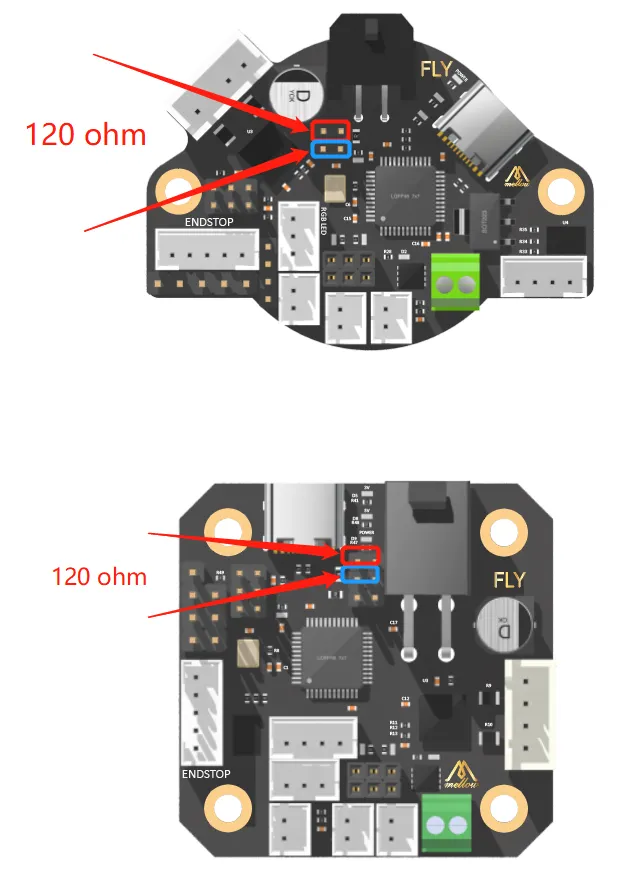
Power Wiring
FLY SHT36/42 does not support power reverse connection protection!!! Please carefully check the power wiring before powering on, do not reverse connect!!! Otherwise, it will damage the SHT36/42 tool board!!!
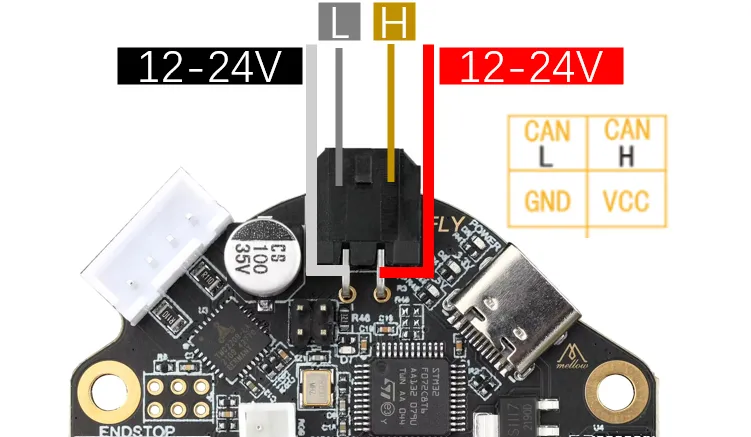
Fan MOS
The fan MOS does not have positive and negative poles, just plug it in firmly
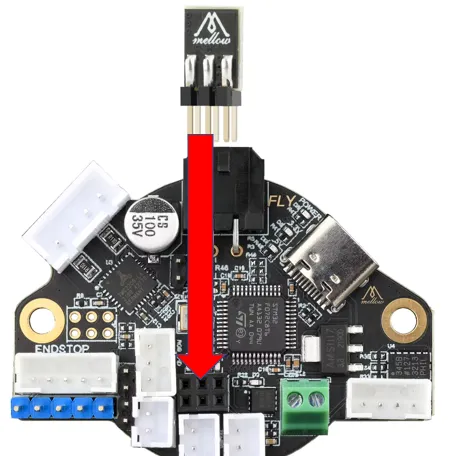
Fan Wiring
SHT36 supports up to two controllable fans, the fan voltage is the power supply voltage, and the wiring method is as follows.
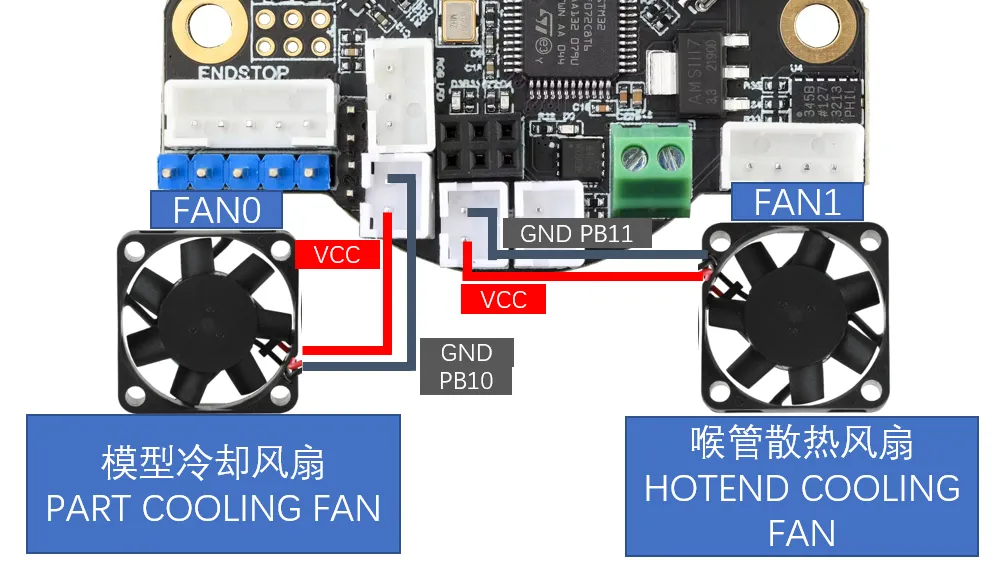
Heating Rod Wiring
The heating rod supports a maximum current of 5A, please pay attention to the power of the heating rod when using it!
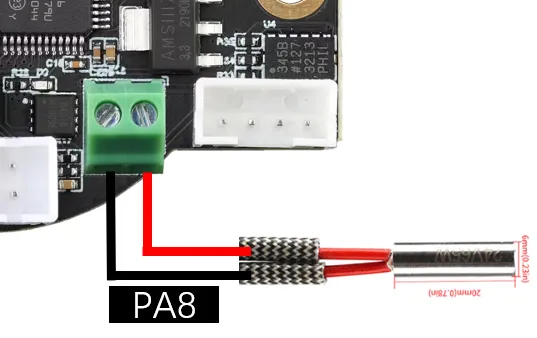
Thermistor Wiring
The following figure shows the wiring method for a common thermistor and PT1000.
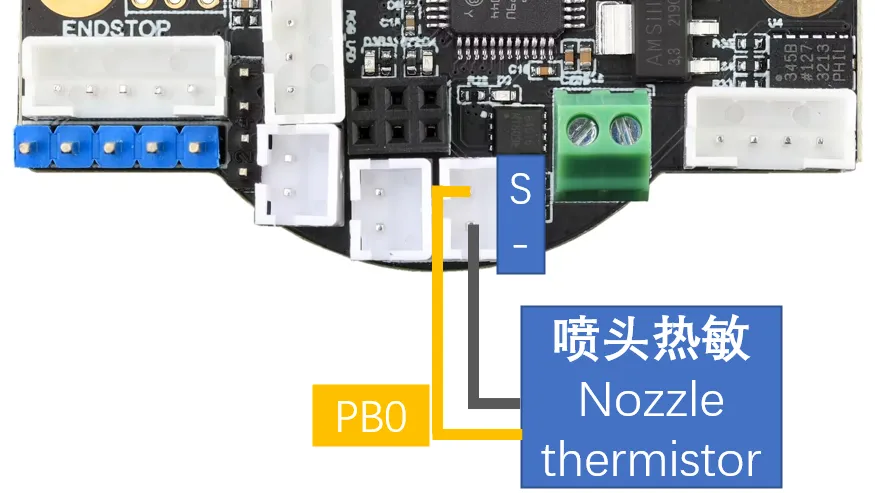
The following figure shows the wiring method for PT100. The default two-wire PT100 only needs to be connected to the 2nd and 3rd pins from left to right.
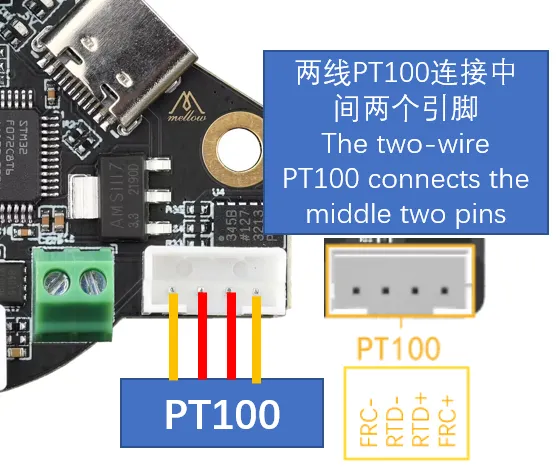
RGB Wiring
The positive and negative poles of the RGB LED beads must not be reversed, otherwise, it will damage the SHT tool board.
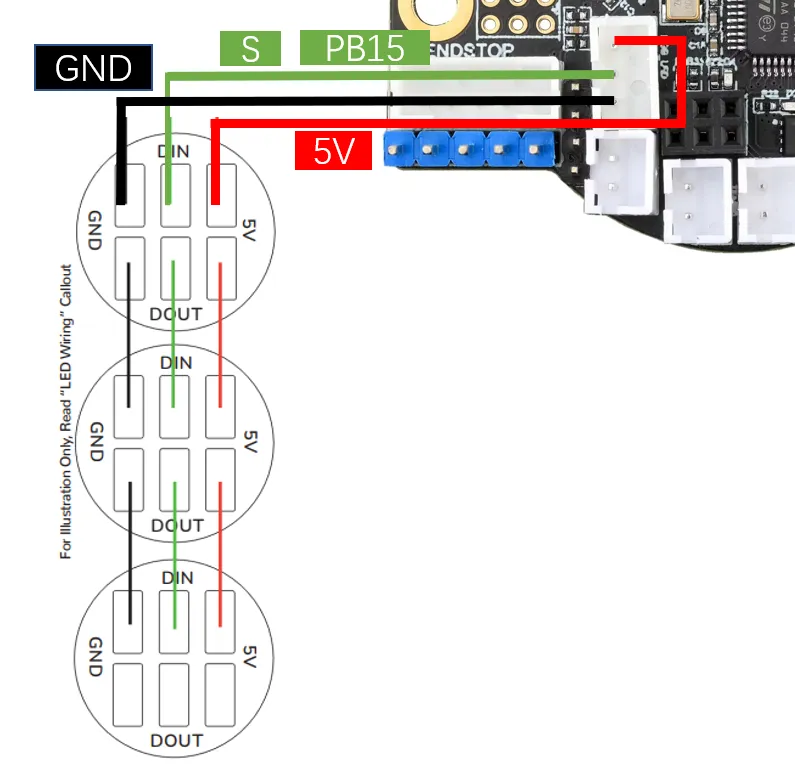
Extruder Wiring
After completing the extruder wiring, please pay attention to configuring the drive current and calibrating the extruder motor direction.
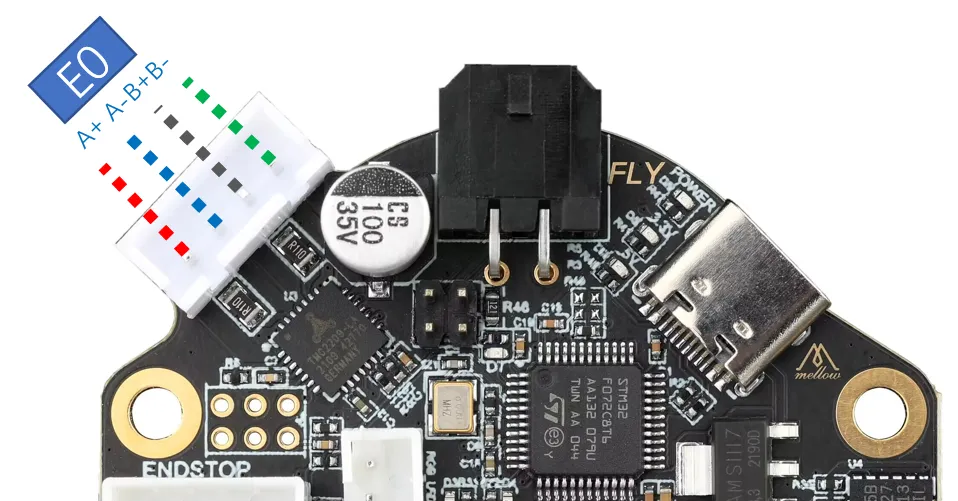
Limit Switch
Limit switches have two types: normally open (NO) and normally closed (NC). Generally, on a 3D printer, it is recommended to use normally closed (NC), so that when there is a problem with the limit switch circuit, the system will report an error in time, which can avoid some unnecessary collisions and damage to the printer.
If it is a VORON model, you can consider changing the installation position of the limit switch, installing the X limit switch on the print head slider, and installing the Y limit switch on the A motor base. In addition, on SHT36, it is recommended to add a ^
before the limit switch to pull up the signal. For example:
[stepper_x]
endstop_pin: ^sht36:PA0 # Add ^ in front to pull up the signal, especially when using PA1, be sure to add pull-up ^
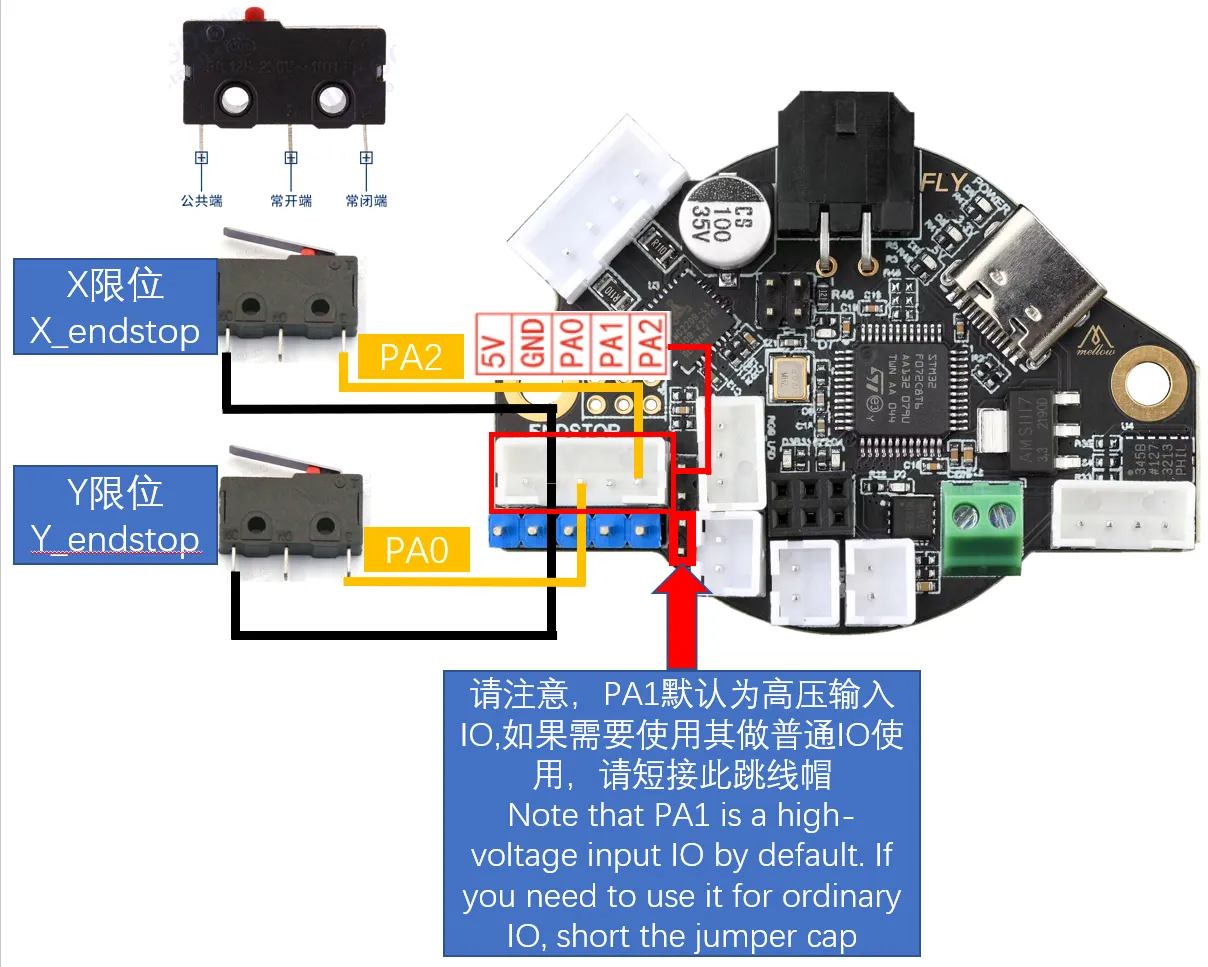
Leveling Sensor Wiring
PB1 only supports PWM signal output and does not support signal input!!! Therefore, it cannot be used as a leveling sensor or limit switch input!!!
Proximity Switch
VORON officially recommends using the Omron TL-Q5MC sensor (previously recommended was PL08N, both have the same principle but different detection distances) for bed leveling.
SHT36/42 does not recommend using proximity switches, you need to connect a separate 12V or 24V power line to supply power to the switch.
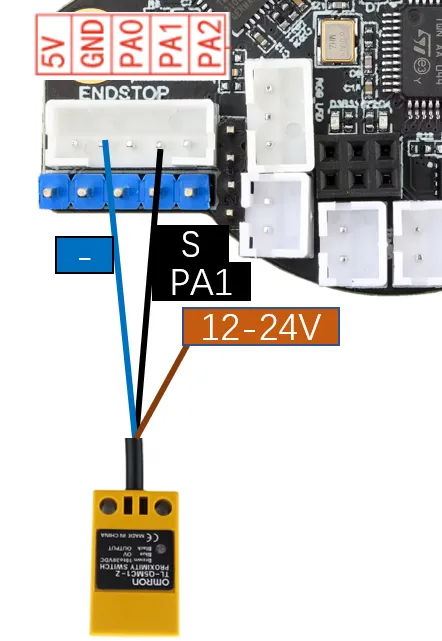
Klicky
Klicky is a third-party leveling sensor that can be made at home at a very low cost, with stable performance and the highest cost-effectiveness, recommended for use. The wiring method is shown in the following figure.
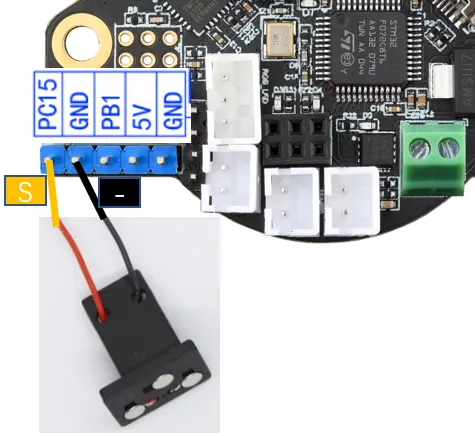
Voron Tap
Voron Tap is the latest leveling sensor solution released by the Voron team, with high precision, strong stability, and good adaptability. When wiring, please note that the positive and negative poles cannot be reversed, otherwise, it will damage the Tap sensor or even the SHT tool board.
Voron Tap is not recommended for 24V, some versions may burn out the Tap sensor when using 24V, this is not a problem with Fly products, but a design flaw of Voron Tap, please be aware!!!
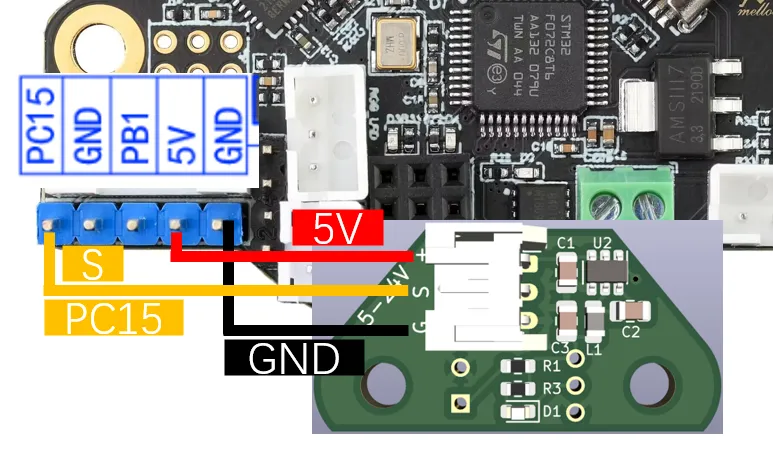
Bltouch
BL-touch has a total of five wires, three for the first group, responsible for the sensor's power supply and probe retraction, the second group for ground and signal lines, outputting limit signals. Please carefully check the wiring order when wiring BL-touch, incorrect wiring may permanently damage the sensor and motherboard!!! The wiring method is shown in the following figure.
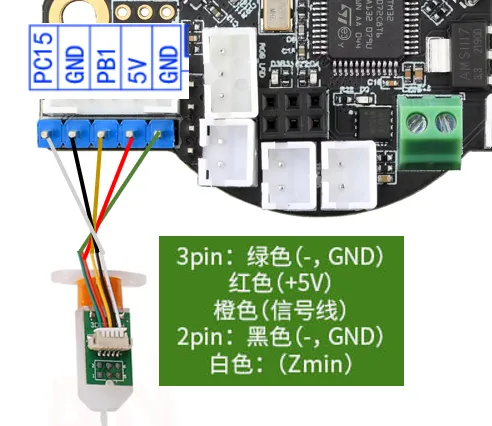
SHT36/42 Connection to UTOC
FLY UTOC is a USB to CAN bus module, which converts the USB port of FLY π into a CAN bus, connecting 3D printing motherboards, SHT36/42, and other CAN bus products through the CAN bus. FLY UTOC has a variety of terminal interfaces on the board, with good flexibility and can adapt to different usage scenarios. In addition, UTOC has been flashed with firmware at the factory, ready to use, no need to flash firmware again.
The following two wiring methods are both acceptable, essentially no difference, just using different terminals.
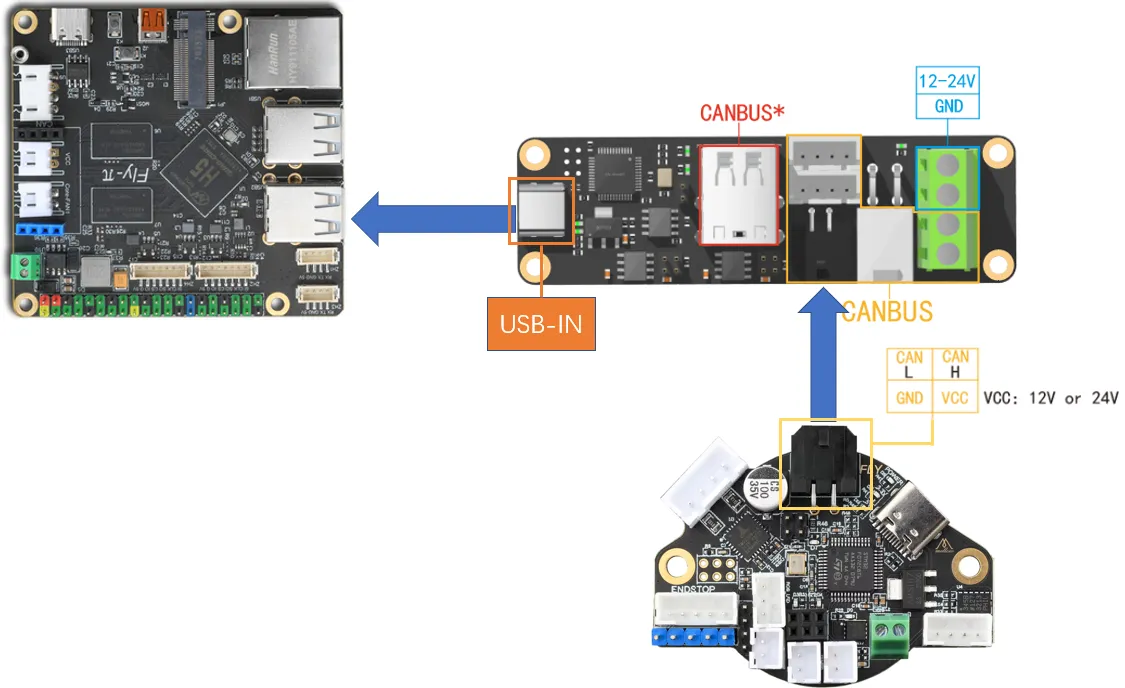
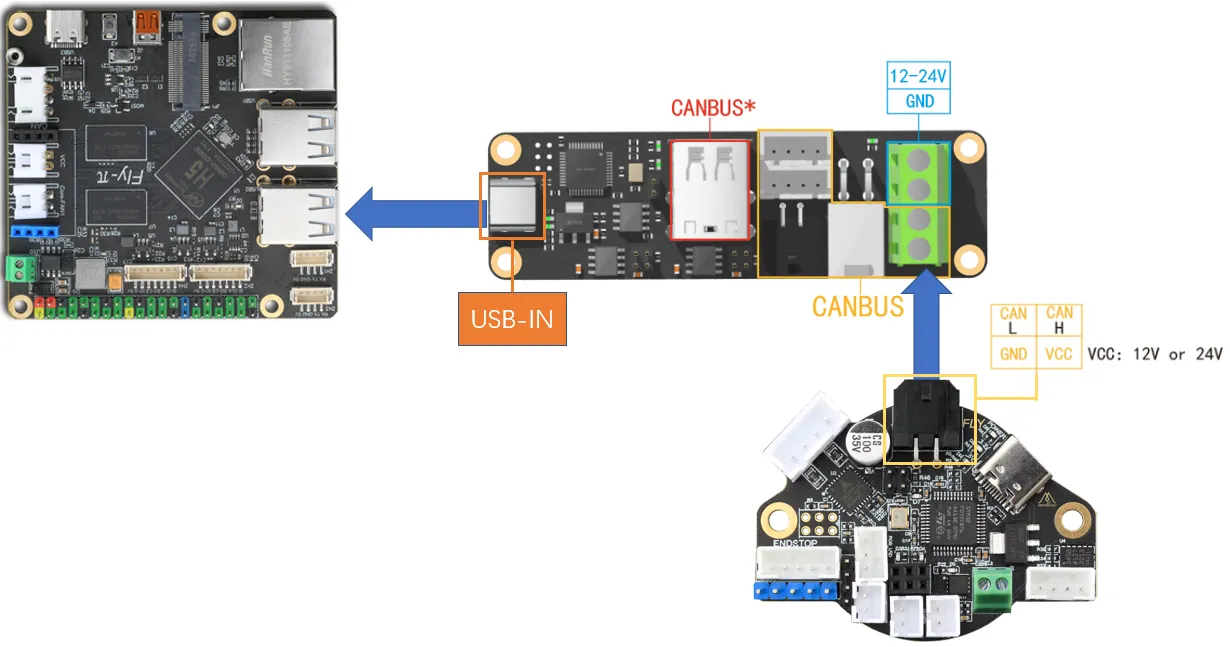
USB-IN: USB to CAN input interface, connected to the host computer
12-24v & GND: Power interface
CANBUS: CAN interface, connected to extended motherboards and tool boards, etc. (connected to devices with on-board CAN transceiver chips)
CANBUS*: CAN interface, connected to extended motherboards and tool boards, etc. (limited to connecting to STM32 device USB interfaces [PA11, PA12], please note to purchase the corresponding version of UTOC)