Mainboard Wiring
Interface Diagram
Interface Description
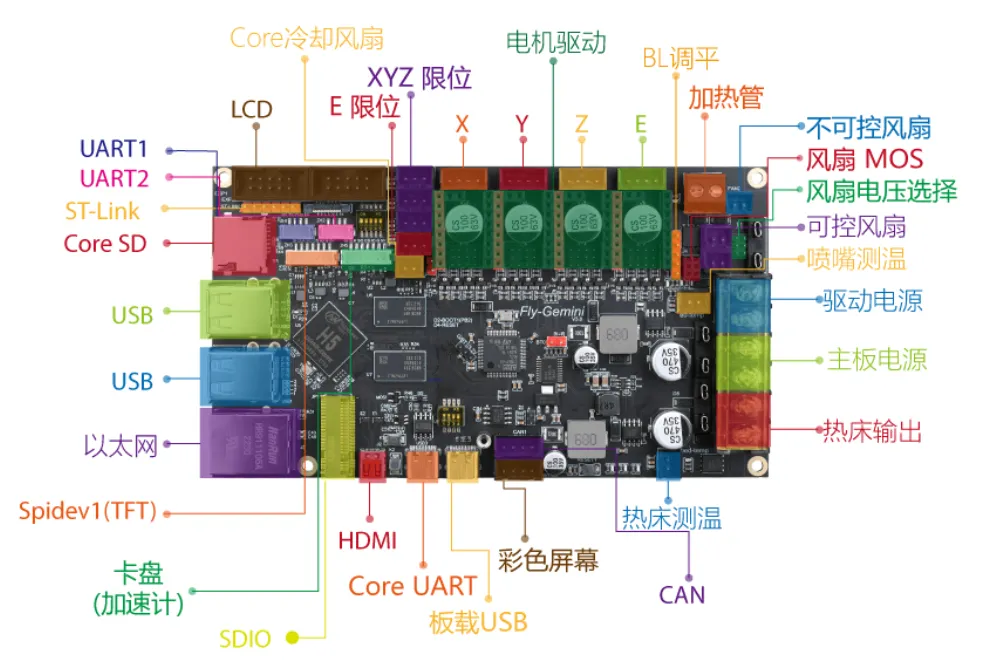
Pin Description
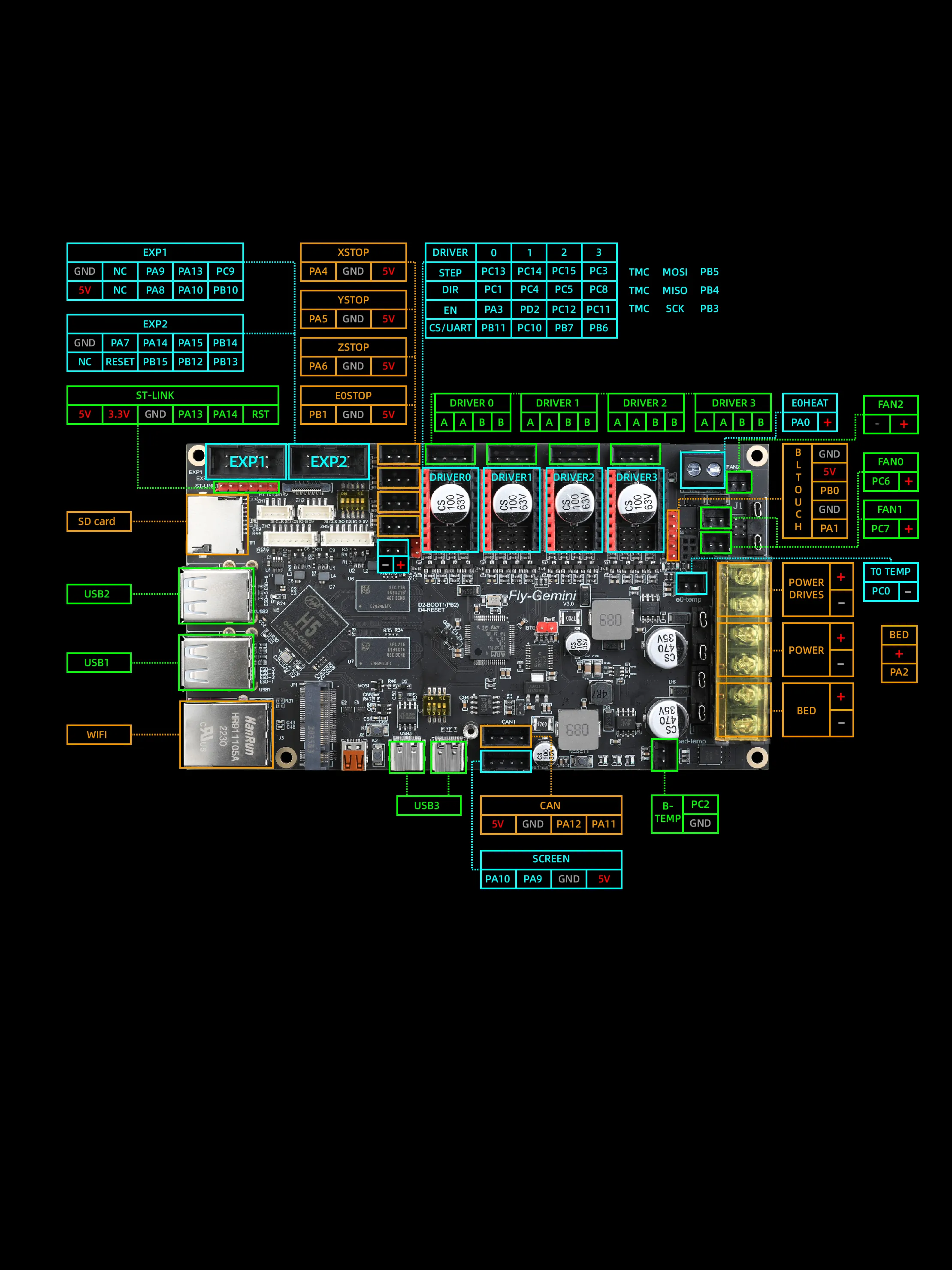
Power Wiring
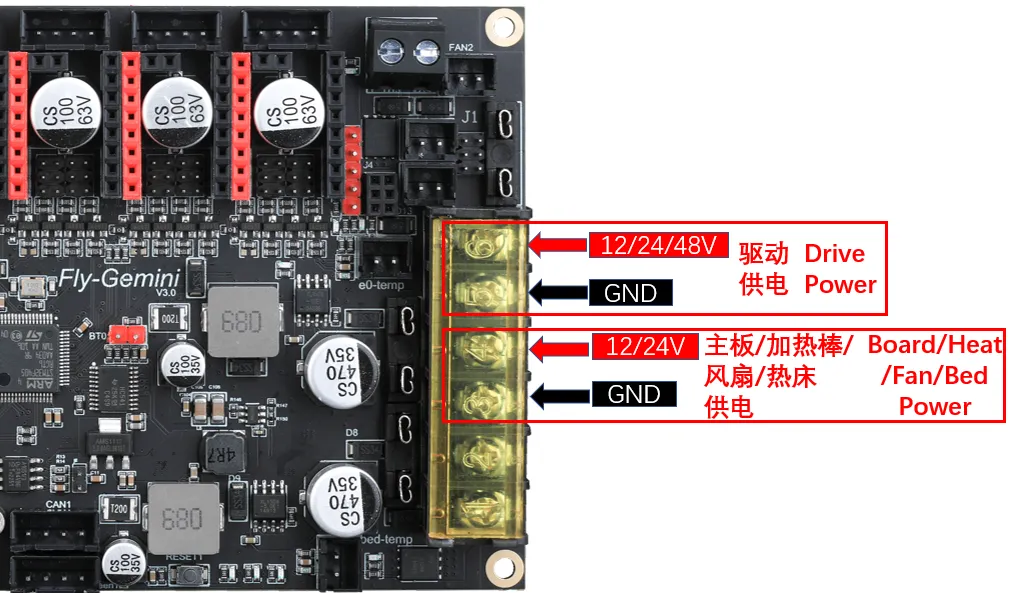
Driver Installation
Mainboard Driver Jumper
-
STEP/DIR Mode. In this mode, subdivision is set by using a jumper cap and current is adjusted by a potentiometer. Most commonly used drivers like A4988 and 8825 require referring to the manufacturer's provided subdivision table and then setting the subdivision through the jumper cap.
-
UART Mode. The most common drivers using this mode are: TMC2208, TMC2209, TMC2226, etc. These driver chips can communicate asynchronously with the main controller via UART, and settings such as subdivision, operating current, and silent mode can be configured by modifying the configuration file.
-
SPI Mode. The most common drivers using this mode are: TMC5160, TMC2130, TMC2240, etc. Similar to the UART mode, settings such as subdivision, operating current, and silent mode can be configured by modifying the configuration file.
Driver Installation
-
Drivers should be checked accordingly before installation to avoid damage to the driver or motherboard.
-
FLY Driver: If the zero-point return function without limit switches is not used, set the DIP switch to position 1; conversely, if the zero-point return function with limit switches is used, set the DIP switch to ON.
dangerous- Caution!!! When installing the driver module, ensure the correct direction is followed, i.e., the EN pin should be at the top left, otherwise the driver and even the motherboard may be damaged!!! Make sure to attach a heatsink to the driver!!!
Stepper Motor Wiring
- Regardless of which manufacturer produces the two-phase stepper motor, its final appearance corresponds to four wires. Regardless of color, whether black, white, green, yellow, they all correspond to four wires. Therefore, we need to group the wires into two groups: A and B.
- For two-phase four-wire stepper motors, there is no need to know which is group A and which is group B, mainly determining one group is sufficient, and the motor direction can be modified in the configuration.
-
In 3D printers, the most commonly used are two-phase four-wire stepper motors, and their principle is shown in the figure below. There are two methods to identify the wire sequence of stepper motors:
- Connect any two phase lines, manually turn the motor shaft, and if obvious resistance is felt, the two phase lines are one group. Conversely, they are not a group, and other phase lines need to be tested.
- Use a multimeter, set it to continuity mode, test any two phase lines of the stepper motor, if they are connected, they are one group; conversely, they are not a group, and other phase lines need to be tested.
Heater Wire Connection
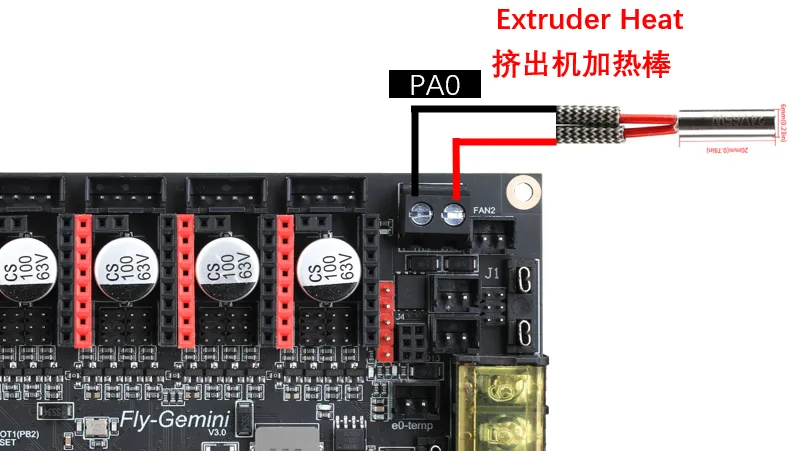
Bed Wiring
-
AC Bed: When wiring the solid-state relay, please pay attention to not connect input and output incorrectly.
-
DC Bed: When connecting a DC bed to the onboard MOS, please pay attention to the power usage. The maximum current for a DC bed cannot exceed 10A. If it exceeds 10A, it is recommended to use an external MOS module to connect the bed, otherwise, it may cause irreversible damage to the motherboard.
Temperature Sensor Wiring
Introduction of Temperature Sensors
-
The wiring method of the temperature sensor is shown in the following figure. Please consult the purchasing merchant for the type of thermistor.
-
If purchased from fly (as shown in the following figure), please configure sensor_type as: ATC Semitec 104GT-2
-
If it is a conventional NTC 100K (as shown in the following figure), please configure sensor_type as: Generic 3950
Mainboard Temperature Sensor Wiring
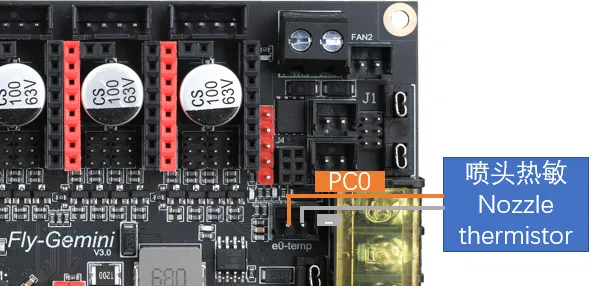
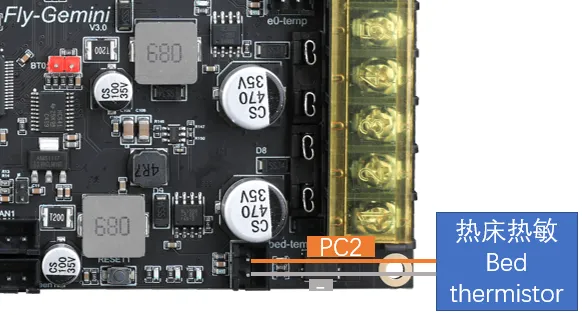
Fan Wiring
-
Fan Wiring
tipVoltage selection for fans. Simply short the corresponding voltage pins with a jumper cap, as shown in the following figure. Note: The jumpers within the yellow boxes in the figure are the same. Caution!! Choosing the wrong fan voltage may damage the fan or MOS module.
- Fan Wiring
Limit Switch Wiring
-
Limit switches have two types: Normally Open (NO) and Normally Closed (NC). Generally, in 3D printers, it is recommended to use Normally Closed (NC). This way, when there is a problem with the limit switch circuit, the system will report an error in time, avoiding unnecessary collisions and preventing printer damage.
Leveling Sensor Wiring
Metal Proximity Switch Wiring
-
VORON officially recommends using the Omron Omron TL-Q5MC proximity sensor (previously, PL08N was recommended; both work on the same principle but have different detection distances) for bed leveling. The wiring method is shown in the following figure.
BL-Touch Wiring
-
BL-Touch has five wires in total, three in the first group responsible for sensor power supply and probe retraction, the second group consists of ground and signal wires, outputting limit signals. Please carefully check the wire sequence when wiring BL-Touch; incorrect wiring may permanently damage the sensor and motherboard!!! The wiring method is shown in the following figure.
Klicky Wiring
-
Klicky is a third-party leveling sensor that can be made at home at a very low cost with stable performance and high cost-effectiveness, recommended for use. The wiring method is shown in the following figure.
-
Project Address: jlas1/Klicky-Probe
Voron Tap Wiring
-
Tap is a Z-probe based on the nozzle, suitable for V2 and Trident printer designs. The entire toolhead moves to trigger the optical switch, providing better accuracy than conventional limit switches and can be used with almost all commercially available print platforms.
warningVoron Tap is not recommended to connect to 24V, some versions may cause the Tap sensor to burn out when using 24V, this is not a problem with the Fly product, but a design defect of Voron Tap, please note!!!
dangerousCaution: 5V and GND cannot be reversed, otherwise the Tap sensor or even the motherboard may be damaged!!!
FLY-Mini12864 LCD Wiring
-
The following diagram shows the wiring method for the FLY mini12864. For screens from other manufacturers, please consult the respective manufacturer. Reversing or misconnecting the Mini12864 screen may prevent the host computer from connecting to the MCU. If you can normally connect to the motherboard's MCU before using the Mini12864 screen but cannot after using it, try unplugging the Mini12864 wiring!!!